Quality control is used in each and every stage of the drug development process. It ensures that the drug product fulfils requirements that include safety, quality, stability and efficacy.
The word ‘quality’ refers to a pharmaceutical drug’s features from both a quantitative and qualitative point of view. It refers to both the quality of the manufacturing process and the product itself.
The word ‘control’ implies a procedure by which production is carried out, according to a specific plan fulfilling the standards previously established.
The word ‘quality’ refers to a pharmaceutical drug’s features from both a quantitative and qualitative point of view. It refers to both the quality of the manufacturing process and the product itself.
The word ‘control’ implies a procedure by which production is carried out, according to a specific plan fulfilling the standards previously established.
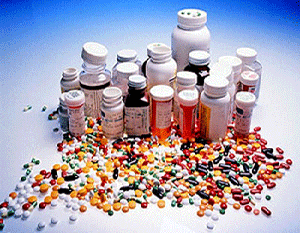
The maintance of drug quality depends on each and every person and the equipment that is used in its development. There is strict supervision in each stage of the process so that the final product achieves its highest quality. The quality control department in a pharmaceutical company is in charge of monitoring records, procedures, systems, facilities, staff and analyses that are made in development and production of a drug product.
Quality variety can occur throughout the process, from the receipt of raw materials to the packaging of the final product. The risk of this happening is increased as the manufacturing method gets more and more complex. Possible causes of diminished quality are:
▣ Methods:
Negligence in the processWrong process
Inadequate process
▣ Materials:
Variations amongst the suppliers of the same substanceVariations amongst batches of the same supplier
Variations in a batch
▣ Staff:
Fatigue and carelessnessLack of interest and attention
Inappropriate training
Unsuitable work conditions
Errors can be controlled, reduced or eliminated by the monitoring of material, its packaging and with good manufacturing practices (GMPs).
Material control starts just after its delivery. Active substances, excipients, packaging and printed materials are stored properly and classified alphabetically or depending on their physical nature.
In the case of active principles the following are examined: their adulteration, percentage purity, expiry date and batch number.
For printed and packaging materials, their weight, colour and grammage are checked too.
In the case of active principles the following are examined: their adulteration, percentage purity, expiry date and batch number.
For printed and packaging materials, their weight, colour and grammage are checked too.
Manufacturing practices control
To achieve the highest quality, the following elements are controlled:- Personnel
- Equipment and facilities
- Production process
- Records
▣ Staff
Staff have to be appropriately educated and trained to work in the pharmaceutical industry.
They have to receive continous training suitable for their role.
They have to be warned about the risks and responsibilities in their role.
The work performed by workers has to be monitored by highly-educated senior managers with broad and deep expertise.
Senior managers always have to be available in case of any potential incident.
They have to receive continous training suitable for their role.
They have to be warned about the risks and responsibilities in their role.
The work performed by workers has to be monitored by highly-educated senior managers with broad and deep expertise.
Senior managers always have to be available in case of any potential incident.
▣ Equipment and buildings
Equipment and buildings must have the right design, size and construction requirements to store, process, examine and package drug products.
Equipment surfaces must be non-absorptive, non-additive and non-reactive.
Equipment must be built and assembled in such a way that it is easy to replace, wash and operate.
Buildings must be free of any kind of contamination.
Equipment surfaces must be non-absorptive, non-additive and non-reactive.
Equipment must be built and assembled in such a way that it is easy to replace, wash and operate.
Buildings must be free of any kind of contamination.
▣ Record control
The most important record controls are related to drug formulation and lot production.
The drug formulation record must contain:- Product name and dosage form.
- Quality by weight or volume of each ingredient.
- Control and manufacturing instructions, specifications and precautions.
- Complete list of ingredients used, including excipients.
- Standards or specifications of each ingredient.
- Complete description of packaging, containers and labelling materials.
The batch production record must contain the following information:
- Lot number.
- Code number.
- Manufacturing date.
- Expiry date.
▣ Production process control
Manufacturing processes are carried out from the delivery of the material through to the final product commercialisation in accordance with a set of rules previously established.
The Master Formula has a full list of all drug components alongside their quantities, procedures, equipment and precautions that must be taken during its manufacturing.

This Master Formula is delivered to the Production Department where all ingredients are re-examined and tested in the laboratory.
Some of these analyses are performed during the production process itself, this is called ‘In Process Quality Control’ (IPQC), which is under supervision of the Quality Control Department.
These tests vary depending on the drug dosage form (syrups, injectables, tablets, semi-solid forms…).
The Master Formula has a full list of all drug components alongside their quantities, procedures, equipment and precautions that must be taken during its manufacturing.

This Master Formula is delivered to the Production Department where all ingredients are re-examined and tested in the laboratory.
Some of these analyses are performed during the production process itself, this is called ‘In Process Quality Control’ (IPQC), which is under supervision of the Quality Control Department.
These tests vary depending on the drug dosage form (syrups, injectables, tablets, semi-solid forms…).
Packaging control
The final product is packaged in its recommended containers avoiding mistakes in labelling or lot number.
Packaging materials are chosen according to the distribution and nature of product.
Packaging materials are chosen according to the distribution and nature of product.
Distribution control
The responsibilities of the Quality Control Department do not finish when the pharmaceutical product is distributed to the market.
The deparment registers samples of each batch and these are stored for years with the purpose of being examined in case of need or demand.
The deparment registers samples of each batch and these are stored for years with the purpose of being examined in case of need or demand.
Organisation of quality control
Generally, there are five different departments in Quality Control:▣ Analytical department
The quality of the final product largely depends on the quality of the raw materials used in the manufacturing process. This department analyses these raw materials and ensures that the drug fulfils a set of specifications to keep its quality. Among these specifications we find:Solubility, viscosity, surface tension, crystal shape…
▣ Chemical testing laboratory
The chemical and physical properties of each lot of raw materials and final products are tested in this laboratory.This laboratory must be located in an isolated area away from noise and vibration and it must have suitable equipment to carry out a wide range of chemical tests.
▣ Biological testing laboratory
Biological examinations analyse biologic drug products and a broad variety of products such as parenteral products which require pyrogen[1] and sterility tests before their commercialisation.▣ Central release office
This office evaluates the many records generated throughout manufacturing and packaging. These records report on the characteristics of each lot produced and distributed in the market, which facilitates the later investigation of potential product quality claims submitted by customers.▣ Inspection and checking
Finally, Quality Control Inspectors are responsible for selecting random samples of raw materials received and final products for their inspection.[1] Agents that cause fever.
Sources: http://thepharmacistpharma.blogspot.com.es/2009/03/quality-control-procedure-in.html
http://www.ancalmo.com/moderno-laboratorio-control-de-calidad/
http://controldecalidadifv.blogspot.com.es/
http://www.aemps.gob.es/industria/inspeccionNCF/guiaNCF/docs/reqBasicosMed/04_capitulo-1b.pdf
http://www.ancalmo.com/moderno-laboratorio-control-de-calidad/
http://controldecalidadifv.blogspot.com.es/
http://www.aemps.gob.es/industria/inspeccionNCF/guiaNCF/docs/reqBasicosMed/04_capitulo-1b.pdf
1 comment
Your opinion matters