In the post titled “Top-down and bottom-up approach” I mentioned that, in order to examine and handle objects at the nanoscale it is necessary to develop devices that enable observation of samples at the atomic scale. These instruments are called scanning probe microscopes (SPMs), from which 3D images are obtained at a very high resolution without damaging the analysed sample (an improvement on electron microscopes (TEMs)).
The scanning probe microscopes are divided, basically, into two types: scanning tunneling microscope (STMs), which we studied in the previous entry within this section, and the atomic force microscopes (AFMs), which we address below.

Atomic force microscopes are based on the following operating principle:
The sample topography is scanned by a microcantilever or strip around a few hundreds of microns (micrometres) long, built in silicon or silicon nitride, whose end has an extremely sharp tip and a curvature radius on the order of nanometers.
When this tip approximates the sample surface, the forces between them produce the cantilever deflection according to Hooke’s law[1].
Depending on the type of tip-sample interaction (whether there is contact or not), the forces measured by AFMs can be: electrostatic, magnetic, capillary forces or Van der Waals interactions...
The deflection that the cantilever experiences is measured by a laser beam focused on the upper surface of this cantilever and reflected in an array of photodiodes that register the laser spot shift.
The sample topography is scanned by a microcantilever or strip around a few hundreds of microns (micrometres) long, built in silicon or silicon nitride, whose end has an extremely sharp tip and a curvature radius on the order of nanometers.
When this tip approximates the sample surface, the forces between them produce the cantilever deflection according to Hooke’s law[1].
Depending on the type of tip-sample interaction (whether there is contact or not), the forces measured by AFMs can be: electrostatic, magnetic, capillary forces or Van der Waals interactions...
The deflection that the cantilever experiences is measured by a laser beam focused on the upper surface of this cantilever and reflected in an array of photodiodes that register the laser spot shift.
In contrast with STMs, AFMs can be used in the study of non-conductive samples, and they can perform two types of measurement depending on the application: image (which, in turn, it is divided into contact mode and dynamic mode) and force.
Contact mode
In this operating mode, the bending of the cantilever is kept constant during the sample scan, hence this cantilever is correspondingly moved up and down to keep invariable the pressure force of the tip on the sample. This up and down movement is registered and a specimen image is obtained.
A relatively fast scan speed and the opportunity to scan rough surfaces are its main advantages. Its principal drawback is that it may damage biological samples (soft and delicate), therefore these samples must be strongly adhered to the surface.
A relatively fast scan speed and the opportunity to scan rough surfaces are its main advantages. Its principal drawback is that it may damage biological samples (soft and delicate), therefore these samples must be strongly adhered to the surface.
Dynamic mode
In the dynamic mode, the microcantilever tip does not come into contact with the sample surface. Instead the strip oscillates at its resonant frequency or just above by a piezoelectric actuator[2] that determines the tip height over the sample.
The tip-sample interaction modifies the resonant frequency and amplitude. Depending on which of these two properties keeps constant during the surface scan, we have:
▣ Non-contact mode where the resonant frequency is stable. This mode is specially indicated for the study of soft biological samples and thin organic films. Because there is no contact, the samples can be subjected to countless analyses without being damaged.
Among its disadvantages, we find its low image resolution and samples must be examined in ultra-high vacuum environments, to avoid the presence of pollutants on the specimen surface that could interfere with imaging.
Among its disadvantages, we find its low image resolution and samples must be examined in ultra-high vacuum environments, to avoid the presence of pollutants on the specimen surface that could interfere with imaging.
▣ Tapping mode where the resonant amplitude does not vary. This method provides high-resolution images of those samples that are susceptible to be easily damaged or are weakly adhered to the analysis surface. The major disadvantage is that the scanning has to be done at a slower speed.
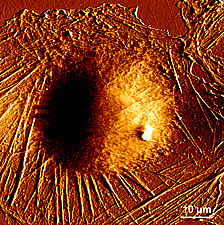
Force mode
In the force operating mode, the tip oscillates vertically while the cantilever deflection is registered.
This method has as its main applications the examination of specific interactions between molecules (antigen-antibody, the complementary strands of DNA), structural interactions (protein folding) or the study of polymer elasticity.
This method has as its main applications the examination of specific interactions between molecules (antigen-antibody, the complementary strands of DNA), structural interactions (protein folding) or the study of polymer elasticity.
[1] This law states that the lenghtening of materials is directly proportional to the applied force on the same.
[2] Mechanical devices whose function is provide force to move another mechanical device.
[2] Mechanical devices whose function is provide force to move another mechanical device.
Sources: http://www.dme-spm.com/funktion.html
https://es.wikipedia.org/wiki/Microscopio_de_fuerza_at%C3%B3mica
http://www.phy.mtu.edu/nue/images/atomicforce/Nanoscope2.jpg
http://slideplayer.com/slide/6856881/
http://www.biozentrum.unibas.ch/research/groups-platforms/overview/unit/lim/
https://es.wikipedia.org/wiki/Microscopio_de_fuerza_at%C3%B3mica
http://www.phy.mtu.edu/nue/images/atomicforce/Nanoscope2.jpg
http://slideplayer.com/slide/6856881/
http://www.biozentrum.unibas.ch/research/groups-platforms/overview/unit/lim/
Your opinion matters